For decades, BMW has been a global force in the automotive industry, known for their fiercely competitive nature both on the track in motorsports and off the track in vehicle production. Years of pushing the limits of technology and engineering is how BMW made its name, and it’s how the brand continues to launch itself forward, delivering to us a new side of BMW and the Ultimate Driving Machine with their iNext program.
As we have previously discussed in some of our articles, the executives at BMW have been formulating a new electrified image for awhile now, a decision that is a key part of BMW’s Number One > Next strategy which involves production of a fully-electric lineup. Although the full lineup is set to debut in 2021, research and test engineers at BMW’s winter test facility in Arjeplog, Sweden have been meticulously perfecting the new electric drivetrain and other electronic technology since February 2019—a feat that is incredibly difficult in such harsh and unforgiving conditions. Through rigorous testing in these extreme conditions, BMW asserts that the new iNext lineup, including the new iX3 and i4, will excel and outperform in all environments, living up to the name of the Ultimate Driving Machine.
More recently, BMW debuted the Vision M Next, an M1-inspired concept car with eDrive motors fixed to each axle and a sensationally powerful mid-mounted four-cylinder engine, good for 600 horsepower and a zero-to-sixty time of three seconds flat. It is these power figures that will influence the future of the electric vehicle market for all BMW vehicles, M models included. Its bold and futuresque design, although an acquired taste for some enthusiasts, was inventive, created from recycled carbon fiber and other materials. The Vision M Next was our first taste of the performance market for BMW’s electrified vision, and foreshadows a new era for BMW.
The next step in iNext production was revealed just a few days ago, with representatives at BMW revealing that a new stage in prototype production has already begun. Prototype production has been occurring in BMW’s Research and Innovation Center (FIZ) in Munich, Germany, within their Pilot Plant. Home to over 850 full-time research scientists, the Pilot Plant is over one million square feet large and capable of assembling and refining both combustion and electric prototypes—a duality that is extremely efficient. When the complete iNext lineup is launched in 2021, it will be manufactured from a line that assembles both combustion and plug-in hybrid models, which is why the Pilot Plant was constructed to mimic the larger, production-level plants with are used to build BMW’s mainstay products in volume.
We’ve come to learn that technology innovation is BMW’s M.O., which is why the prototype production plant in Munich serves as one of the most technologically-advanced facilities that we have ever seen from BMW. Divisions within the plant include a full-service body shop, prototype and concept model construction area, and a 3D modeling centre. If you thought that wasn’t impressive enough, BMW is employing the use of lasers and augmented reality to perfect prototypes before production—talk about revolutionary.
Vehicle sections are joined together by a rotary bonding process, which occurs when a steel part pierces an aluminum part and the resulting frictional heat energy fuses the two components together, creating an astonishingly strong bond. Lasers and computer-aided design (CAD) software are then utilized to scan the surfaces for imperfections, documenting information of any defects and relaying it back to an augmented reality app, which then juxtaposes information from both the CAD model and real-life measurements.
Executed by groups of robots, BMW also uses computer tomography to take X-rays of already assembled vehicles to view the status of internal components without having to dismantle the whole vehicle. These innovations not only increase efficiency between the multiple divisions of the Pilot Plant, but also reduce complexity, allowing for the prototypes to be assessed for completion quicker and more accurately, foregoing previously tedious quality-control methods.
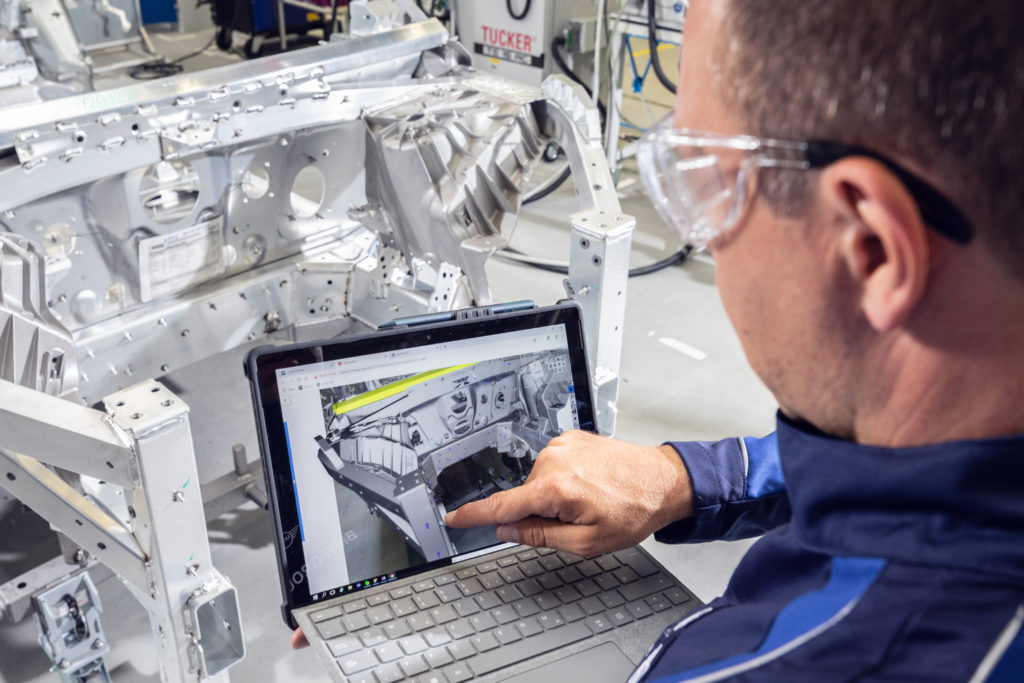
A BMW researcher using an augmented reality app to compare the bolts of the floor assembly with the CAD model.
The future of iNEXT is not straying from the Ultimate Driving Machine that we are used to, it’s simply redefining it. With new rumored leading-class integrations like driver assistance systems, electric drivetrain connectivity features, and level 3 automated driving, the iNEXT lineup, as BMW puts it, “embodies the future of driving pleasure in a particularly comprehensive way.” The new iNext program proves that the Ultimate Driving Machine isn’t going anywhere—it’s merely evolving.—Malia Murphy
[Photos courtesy BMW AG.]