Note: This article was written for BMW by Jackie Jouret, who also serves as Features Editor for BMW Car Club Magazine: BimmerLife.
In South Carolina, history can be divided into two epochs: Before BMW, and After BMW. BMW’s own history can be similarly divided: Before Spartanburg, and After Spartanburg.
The dividing line between each period is June 23, 1992, when BMW announced that its first full production plant outside Germany would be built in Spartanburg, South Carolina. (BMW’s plant in Rosslyn, South Africa wasn’t yet a full production plant.) Leading up to that announcement, BMW executives had recognized the need to expand beyond Bavaria if the company were to continue to thrive.
It wasn’t a new idea—in 1961, BMW had explored a manufacturing partnership with American Motors—but it gained traction in the 1980s. Following the decoupling of the US dollar from the gold standard, exchange-rate fluctuations were making German imports more expensive in the US just as new Japanese marques began offering premium cars at much lower prices than BMW or Mercedes. BMW countered by reducing prices, but it wasn’t enough.
“The Board of Management realized that they were going to have to leave Germany with some production for other parts of the world,” said Carl Flesher, then BMW of North America’s VP of Marketing. “That was a huge decision, but boy did they make the right one.”
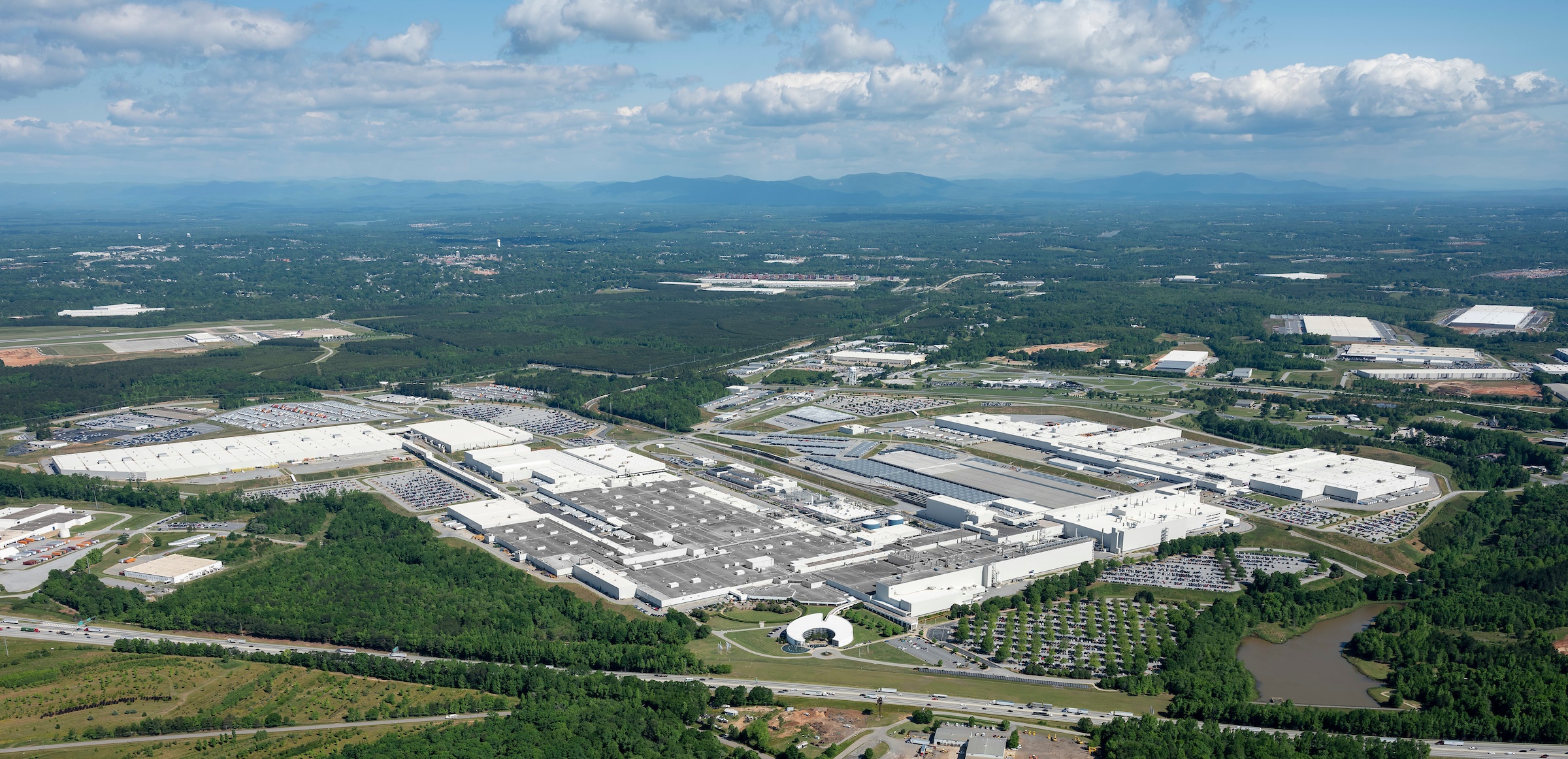
Aerials 5/7/21 – File: 050621GR56
“We ended up in South Carolina because of the port operation, and we had planned to settle the manufacturing operation just outside of Charleston until Governor Carroll Campbell told us that was a mistake,” Flesher said. “He said hurricanes hit there and our standing inventory would be in a lot of trouble.”
Campbell suggested the Upstate region, about 200 miles northwest of Charleston. The Upstate was South Carolina’s traditional manufacturing corridor, known for nearly a century as the Textile Capital of the World. By the late 1970s, however, most of its 40 mills had closed, unable to compete with lower-priced textiles from China and other emerging markets.
“We had hard times,” says Bobby Hitt, then managing editor of the Columbia Record in South Carolina’s capital. “This was an area that had lost over 60,000 jobs to the textile industry leaving, and there were a lot of stores boarded up.”
The Upstate was well situated, with major rail lines and Interstate 85 running through Greenville, Spartanburg, and Anderson counties. That infrastructure had already inspired Michelin to relocate its North American headquarters from New York to Greer, South Carolina in 1985, and to place seven of its 15 production plant in the state.
“Panke worked with the governor’s office and found a location in Anderson next to a railroad track, where the acreage was large enough for us to build and expand,” Flesher said. “Then [Board Chairman Eberhard] Mr. von Kuenheim flew to the US with Panke to see the site, and he told Panke that this wasn’t where BMW needed to be. He said we need to be on the interstate, we need to be visible, and we need to be next to the airport.”
One site met von Kuenheim’s criteria, but it already had 250 homes on it. “The governor’s office went to every single one of those homeowners, and they all agreed to move,” Flesher said. The houses were either moved to new locations or purchased so their owners could purchase another house elsewhere, and no exercise of eminent domain was required. “I thought, ‘Wow, South Carolinians are not built like New Yorkers.’ What a sacrifice.”
South Carolina’s Ports Authority as well as the state and county governments spent $36.6 million buying the 900-acre plot, then spent another $90 million on highway development, an airport expansion, job training, and a 20-year flat rate for water and sewer services at the plant.
“At the time, people thought South Carolina had given away the store, that we’d been taken to the cleaners by BMW,” said Hitt. “I think now, people have come to realize that the greater risk was taken by BMW, coming to a place that was so unknown.”
It may have been unknown, but BMW did its research. As Panke’s team discovered, South Carolina had another crucial ingredient for successful manufacturing: a network of 16 technical colleges, which could help supply the skilled workforce BMW needed to build automobiles.
“The planners at BMW said they looked at the technical education system in South Carolina and saw it as the best in the country, that it had the ability to create skill in its people,” Hitt said. “They also rode around in the neighborhoods—I love the way Germans do this—and looked at how people lived. They kept their houses and their cars neat, and that meant they were prideful. And if you take skill and pride, you can build a BMW.”
BMW’s decision to build a new plant in Spartanburg, South Carolina was announced by Governor Campbell and Chairman von Kuenheim on June 23, 1992. The night before, the news broke on WYFF television by senior correspondent Kenn Sparks, who’d been given the scoop by Campbell. (Sparks would later join BMW Manufacturing as an Internal Communications Manager.)
“Nobody knew what it meant, quite honestly,” Sparks said. “Even Governor Campbell didn’t grasp the scale. But what he did grasp, and this was the ultimate goal of his administration, was that this was not just an automobile plant. He said, ‘Kenn, we are bringing the auto industry to South Carolina. When an auto plant comes, an industry comes with it, and it is going to have profound effects across the state.’”
First, BMW had to build a factory, for which it estimated the cost at $400 million. On September 30, 1992, Governor Campbell and Chairman von Kuenheim broke ground for BMW’s first full production plant outside of Germany.
“The groundbreaking in Spartanburg is still a vivid memory for everyone who participated,” said Tom McGurn, then BMW NA’s Corporate Communications Manager. “The dealers drove 7 Series from a dealer meeting in Atlanta, and as we crossed into South Carolina we left the interstate for a rural road. There were people holding signs welcoming BMW to the state, and as the caravan reached Greer the main street was completely lined with welcomers, even a high school band.”
During the ceremony, Campbell declared the occasion “symbolic of a new era focused squarely on the next century of progress” for South Carolinians, while von Kuenheim pronounced it the same for BMW.
“The decision that takes us to America is a major step for BMW,” said von Kuenheim. “We know it is the right decision in view of the future demands. The right people for the task are already right here where we need them. Together, ladies and gentlemen, we shall make automobiles from South Carolina famous throughout the world.”
Construction of the plant took just 23 months, during which BMW began hiring management and assembly workers. In April 1993, Panke was named chairman and CEO BMW (US) Holding Corp., which gave him responsibility for BMW of North America as well as BMW Manufacturing; he’d hold that position until July 1995, when he returned to Munich as BMW AG’s executive director.
Interestingly, the production team would be led not by personnel from Germany but by executives recruited from Honda of America Manufacturing in Ohio: Allen Kinzer and Edwin Buker. Kinzer would serve as BMW Manufacturing’s first president, with Buker as VP. The two were chosen for their expertise in running a foreign automaker’s plant in the US.
BMW has never discussed whether South Carolina’s traditional antipathy toward labor unions had worked in its favor during the site-selection process, but the decision to eschew the UAW wasn’t about saving money. At Honda, Kinzer and Buker had fostered greater cooperation between management and labor than was customary in unionized auto plants which lead to higher production quality, which Panke declared a goal at BMW, as well.
BMW had no trouble attracting nearly 100,000 applicants in its first round of hiring. From those, approximately 570 were selected, with that number expected to increase to 2,000 by the year 2000.
As Honda had done in Ohio, BMW Manufacturing would begin production with an existing model, the four-year-old E36 3 Series sedan. “It was a known quantity[MO1] [OS2] , and we would know if we were building them right or not,” said Flesher, who became BMW Manufacturing’s first vice-president of public relations in 1992. “We had to build a lot of cars before the assembly line settled down and could do it consistently.”
The first complete car rolled off the line on September 8, 1994, bearing the signatures of every associate at the plant. Two months later, on November 11, 1994, that car would be driven onstage by Sky Foster, Associate number 5, who’d joined BMW Manufacturing’s human resources department in 1993 and went on to serve in Corporate Communications until the end of 2021.
“The company was small enough at that point that every person who worked there fit on the stage,” Sparks said. The presentation was followed by fireworks and a reception at the Zentrum, attended by all of the associates and luminaries including Pischetsrieder in his new role as chairman of the board of management, Panke as new BMW NA CEO, supervisory board chairman Hans Graf von der Goltz, and Johanna Quandt, the widow of BMW principal shareholder Herbert Quandt, who’d died in 1982. For Mrs. Quandt, especially, it was momentous occasion.
“Mrs. Quandt was beside herself with joy,” Sparks said. “She was so happy seeing the factory, the associates, the first car, and all of that. She was so heartfelt in saying, ‘I wish my husband Herbert Quandt were alive to see this. This is something he always wanted.’ I asked her what she meant, and she said he was so grateful to the US for the Marshall Plan that rebuilt Germany after World War II, and he’d always wanted to show his gratitude for what the US had done for Germany. It still chokes me up, just remembering that, because it was so much from her heart.”
Having established its competence with the 3 Series, BMW Manufacturing was soon ready to begin building an all-new car: the roadster.
In May 1993, Pischetsrieder had succeeded von Kuenheim as BMW Board Chairman. While BMW’s new roadster was under development, he suggested that it be assembled at Spartanburg. “Pischetsrieder said it looked like what we should be building there,” Flesher said. “It’s adding to the brand, not just repeating what we’re already building.”
Z3 production began in September 1995, followed shortly by the car’s debut in the James Bond film GoldenEye. By the time production ended in July 2002, Spartanburg had turned out 297,088 examples, of which about 40 percent were sold in the US. The Z3 attracted a devoted following, and in 1997 its owners began gathering for Z3 Homecomings at the plant and the Zentrum.
The Zentrum and its 200-seat auditorium had already become popular as an event space for the local community following its opening in 1995, as well as a training center for new associates and a staging ground for plant tours.
“Panke decided to build the Zentrum, and the concept was that the plant needed to introduce itself to its new neighbors,” said Sparks, who was in charge of the Zentrum during his tenure at BMW Manufacturing. “Mobile Tradition (now BMW Group Classic) was just getting underway, and Pischetsrieder instructed Christian Eich [Head of Mobile Tradition] to give the Zentrum the right selection of historic BMWs that would show off the history of our company. We also borrowed cars from enthusiasts, and we built our own historical exhibit on the models assembled at the plant, including the James Bond Z3 from GoldenEye.”
Four years later, the Z3 would be joined by another model exclusive to Spartanburg: the X5. As BMW’s first Sports Activity Vehicle, the X5 was aimed squarely at American tastes, though its global success would end up spawning an entire series of X vehicles, turning the Spartanburg plant into BMW’s center for competency for SAVs worldwide.
Since 1992, BMW has invested $14.8 billion dollars in its Spartanburg plant, and what began as a single assembly hall building 3 Series sedans and Z3 roadsters is now an eight-million square foot colossus. It’s BMW’s largest production plant worldwide, surpassing even the home factory in Munich for volume. Production has grown from 28,000 vehicles per year to a 433,810 per year record in 2021. Plant Spartanburg is currently capable of producing up to 450,000 vehicles per year. (Following the end-of-production of the first-generation Z4, roadster production was moved to Germany.)
Spartanburg builds X3, X4, X5, X6, X7, and XM models, including models with hybrid powertrains. Starting in 2026, those vehicles will use batteries assembled at a $700 million plant in nearby Woodruff. That will coincide with production of battery-electric variants of BMW X vehicles.
Drivetrain flexibility was pioneered at Spartanburg, which has the ability to build vehicles with gasoline or diesel combustion engines, plug-in hybrid powertrains, or fully electric drive on the same assembly line.
The innovations don’t stop there. In the body shop, Spartanburg was BMW’s first plant to employ a new optical measurement system that streamlines the entire production process. Digitalization is also reaching new heights at Spartanburg, allowing more precise logistics within the just-in-time production process. That process now includes sheet-metal stamping, which came online at Spartanburg in 2024 after three decades of outsourcing.
Spartanburg was BMW’s first plant to use cooperative robots, which work together with humans to build the automobile. Previous assembly robots had to be isolated from humans because of the potential for injury or even death. New sensors allow humans and robots to work together, because the robot can now sense when its movement might injure a human worker. Today, the plant is testing humanoid robots, which might one day relieve human associates from repetitive or ergonomically challenging tasks. Toward that end, Spartanburg was first to equip its associates with exoskeletal supports, helping to reduce the physical strain of assembly work.
Even as its vehicles were created to suit American tastes, exports have figured prominently in the Spartanburg business plan since the beginning. The BMW X models have become increasingly popular worldwide, and currently more than half of production is exported to 120 countries around the world, making Spartanburg the largest vehicle exporter by value in the United States (value of $10 Billion in 2024). At the same time, Spartanburg-assembled vehicles now constitute more than 50% of all BMWs sold in the US.
Sustainability has also been part of the mission from the outset, particularly with respect to renewable energy and reduced CO2 emissions. The plant gets about 20 percent of its energy requirements from methane gas generated by the Palmetto Landfill, which is connected by a 9.5-mile pipeline to BMW Manufacturing. There, it’s converted into electricity and heat for the plant’s operations. Elsewhere, the plant uses hydrogen fuel cells to power the automated tuggers that move parts and other supplies along the line.
As the plant and production have grown, employment has increased dramatically, too: from 570 employees in 1994 to more than 11,000 in 2024. So has the supplier base. Where BMW Manufacturing had hoped to attract nine local suppliers, the plant is now served by more than 60 Tier 1 suppliers in South Carolina alone, and around 300 throughout the US. Those suppliers include ZF (transmissions and axle systems), Magna (steel), DAA Draexlmaier (dashboards), and Sage Automotive Interiors (upholstery) that have set up nearby to serve BMW’s just-in-time manufacturing process.
A 2023 study by the University of South Carolina’s business school found that BMW Manufacturing was responsible, directly and indirectly, for nearly 43,000 jobs in the state, paying $3.1 million in wages and salaries as part of its annual economic impact of $26.7 billion. That wouldn’t have materialized if BMW had chosen another location for its first full production plant outside Germany. Instead, BMW’s investment inspired Boeing, Mercedes, and Volvo to set up their own production plants in South Carolina, compounding the economic impact.
“The presence of BMW has changed everything in the trajectory of the future in this state,” said South Carolina Governor Henry McMaster. “It has created a manufacturing renaissance in South Carolina which is unequalled in any other state.”
BMW changed South Carolina, without a doubt. At the same time, South Carolina has changed BMW, turning it from a small Bavarian automaker into a global powerhouse, and one of the most recognized brands worldwide.
“When we made the decision to build this plant, the entire company was the size this plant is today,” said Oliver Zipse, chairman of the board of management.
Indeed, the 1993 output of BMW’s factories in Germany and South Africa numbered just 532,960 vehicles, and its total workforce consisted of 71,043 employees. Three decades later, those two factories have been joined by plants in the US, Mexico, Brazil, India, China, Thailand, and the UK, plus additional locations in the European Union, whose 154,950 employees assembled 2,554,183 BMW, MINI, and Rolls-Royce automobiles in 2023.
BMW’s globalized manufacturing network helps to insulate the company from currency fluctuations worldwide, and it also gives the company a strong foundation against increasingly nationalistic trade policies (i.e. tariffs). It also allows BMW to better withstand supply-chain disruptions, like those that resulted from the global pandemic of 2020-2021. As a result, BMW’s profitability has risen from DM 516 million ($311 million) in 1993 to €17.1 billion ($18 billion) in 2023.
BMW’s investment in Spartanburg represented a commitment in the US market, one that paid off handsomely. Having sold just 65,683 vehicles in the US in 1993, BMW of North America sold 371,346 in 2024—another record year. That’s a nearly sixfold increase, one that neatly quantifies the After Spartanburg era at BMW, as well as the After BMW era for South Carolina.