Last week, I drained the oil in the FrankenThiry’s Behr “wing cell” compressor and found it was filled with black particulate matter. In the post, I said the particulates “were likely from the seals in the compressor itself, but I suppose it’s remotely possible that they could’ve originated elsewhere and been transported there in the oil.” I was wrong on both accounts.
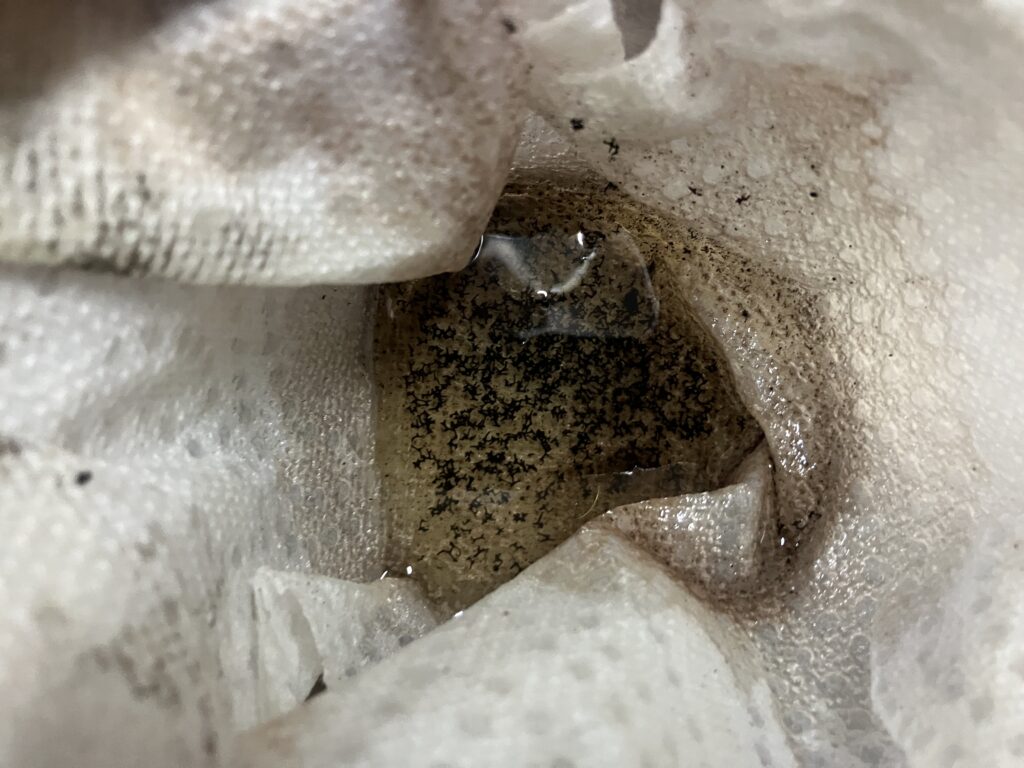
The particulate in the oil I discovered last week.
I suspected that the “dissolved seals” hypothesis was wrong when I fished some of the material out, blotted off the oil, looked at it with a magnifier, and saw what appeared to be a foam-like structure. It turns out that these wing cell compressors (some of them? all of them? not sure.) had a foam gauze-like pad inside, located between the housing and the compressor innards, whose purpose was… exactly what? Not only can I find no definitive technical information from Behr on it, but I’ve only found a few references to the foam. Most of them are from a single poster, “Johnn635,” in South Wales, who posted questions about it on several different forums while attempting to rebuild his compressor in 2017. He hypothesized, “My best guess is that it serves to hold the oil in such a way that the outgoing compressed gas is in contact with as much as possible, promoting oil circulation and preventing ‘pooling’ in the bottom of the compressor” and proposed replacing it during his rebuild with a stainless steel pot scrubber. Another poster said, “The “gauze” is an absorber for refrigerant oil which seeps past the shaft seal and could initiate clutch slip if not stopped.” Jay Stratton, who some of you know from his website, www.jaysbmwparts.com, and his business rebuilding brake boosters, power steering pumps, compressors, and other parts, first commented, “I would not worry about it,” but then said,”The metal scouring pad is a good idea.”
If you look at the comments to last week’s piece, you can see that two readers knew what the black bits were from. Carlos Perez wrote, “For some long-forgotten bright idea, many of those wing cells (I prefer “tin can”) had a factory-fitted clump of plastic/fiber (?) mesh at the rear of the compressor. Couldn’t see it working as a filter of any kind, maybe intended to sort of condense or retain oil, or possibly just to harden, become brittle and spread its bits into the system.” Federico Molina said, “Like Carlos commented, that debris in the oil looks like the foam that goes inside the compressor. I found you can buy it as aquarium filter foam and I used it when attempting to rebuild my wing cell.” Who needs deep web searches of user forums when my readers bring the expert truth to my doorstep? (Seriously, thanks, Carlos and Federico.)
My knowledge about the role of oil in a/c systems is that the lubrication oil is miscible with the refrigerant (it dissolves in it), and thus is carried throughout the system. Still, the compressor is the component that has the moving parts requiring lubrication, so having some sort of absorbent block in the bottom to hold oil there to ensure compressor lubrication doesn’t strike me as a bad idea. Until it breaks up and contaminates the system.
Mr. Molina added, “Eventually, I got tired of messing with it and built my own Sanden bracket, LOL (yet another M30 Sanden bracket @ mye28). It might make sense for you to try and fix the wing cell on the cheap, but I would not recommend it to anyone these days.”
I agree with Mr. Molina. The path for any sane person would be to throw the compressor in the recycle bin, buy a $90 Chinese-made Sanden clone and a bracket to bolt it to the M20 engine, deal with whatever fitting fettling and hose fabrication is necessary to adapt the existing hoses to the Sanden and smile at the resulting a/c system that then reliably pumps out cold air.
I, however, am not any sane person. But you already knew that.
Seriously… as I’ve said over and over, none of the cars ever get everything they need, time-wise or money-wise, but especially money-wise. It makes sense to me to try and save the likely $300-ish it would cost me for a compressor and a bracket by trying to rebuild the compressor and see what happens. All I lose is a few evenings, and even that’s not a loss, as I get a few articles and a hearty “well, I’d never do that again” to put in my bag of stupid stuff I’d never do again.
So in I went. Finding an exploded compressor diagram took me quite a while, but I located one on page 144 of the 2013 Santech catalog here. A screen capture of the important section is below. Johnn635 referred to the foam as visible but unlabeled in the parts diagram, but I don’t see it.
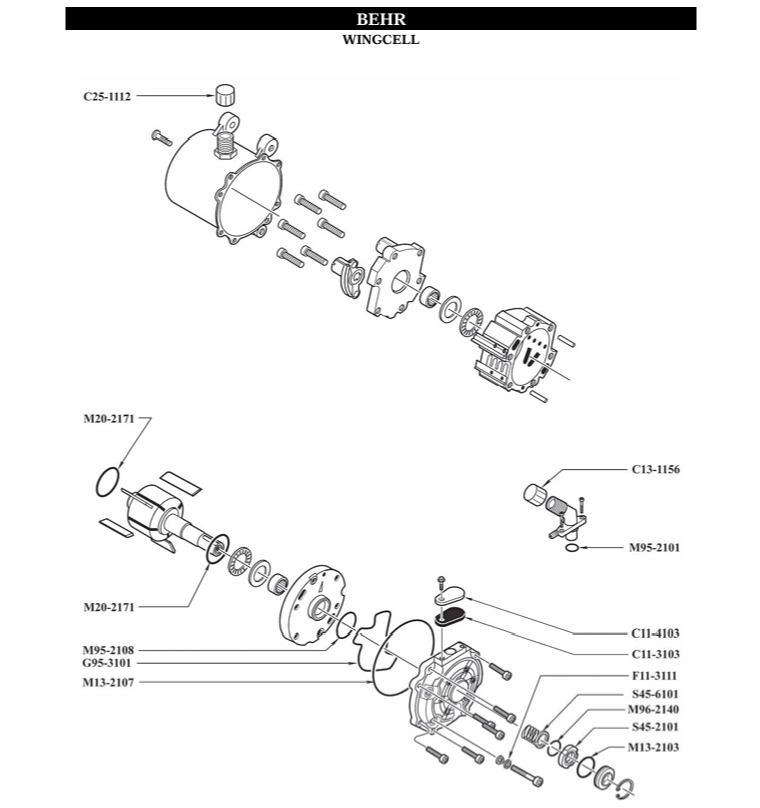
Pretty neat.
This post on BimmerForums is a wonderfully well-photographed how-to on compressor disassembly, though it’s a little short on specifics. First, the outer clutch plate needed to come off. I spun off the nut, holding it on with an impact wrench, but there was no obvious way to pull off the plate. The photo in the article showed the insertion of what looked like a screwdriver between it and the pulley, but a few other posts on online forms strongly advised against that, as it was likely to bend the pulley. With nothing to lose, two screwdrivers on opposite sides were brought to bear, and the plate eventually lifted up. The pulley looks straight to me.
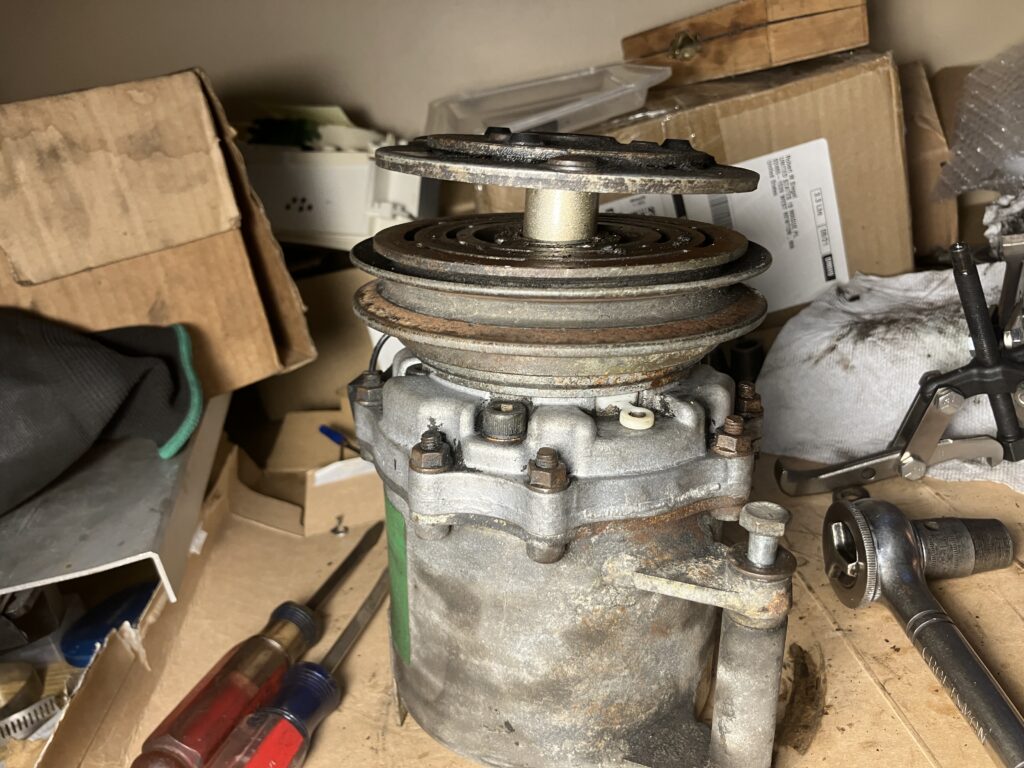
Yes, that’s a puller in the background. No, it didn’t work, as it couldn’t really push off against the post in the middle.
Next, the nut and washer holding on the other clutch plate needed to be undone by positioning a screwdriver on one of the notches and smacking it with a hammer.
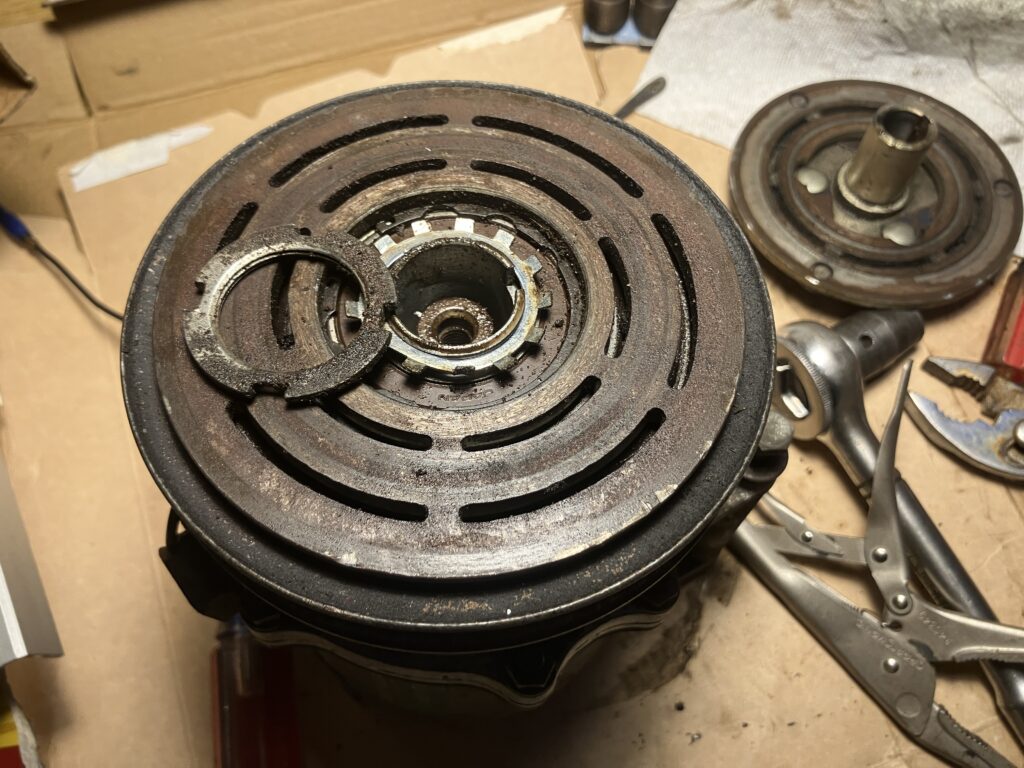
The lower clutch plate and pulley.
You’ll see a big circlip in the middle of the lower plate. It holds the clutch bearing in place unless you need to replace the bearing, leave the circlip alone, and lift the bearing, plate, and pulley together. With it removed, you see the clutch coil, the thing that’s energized when the a/c is turned on.
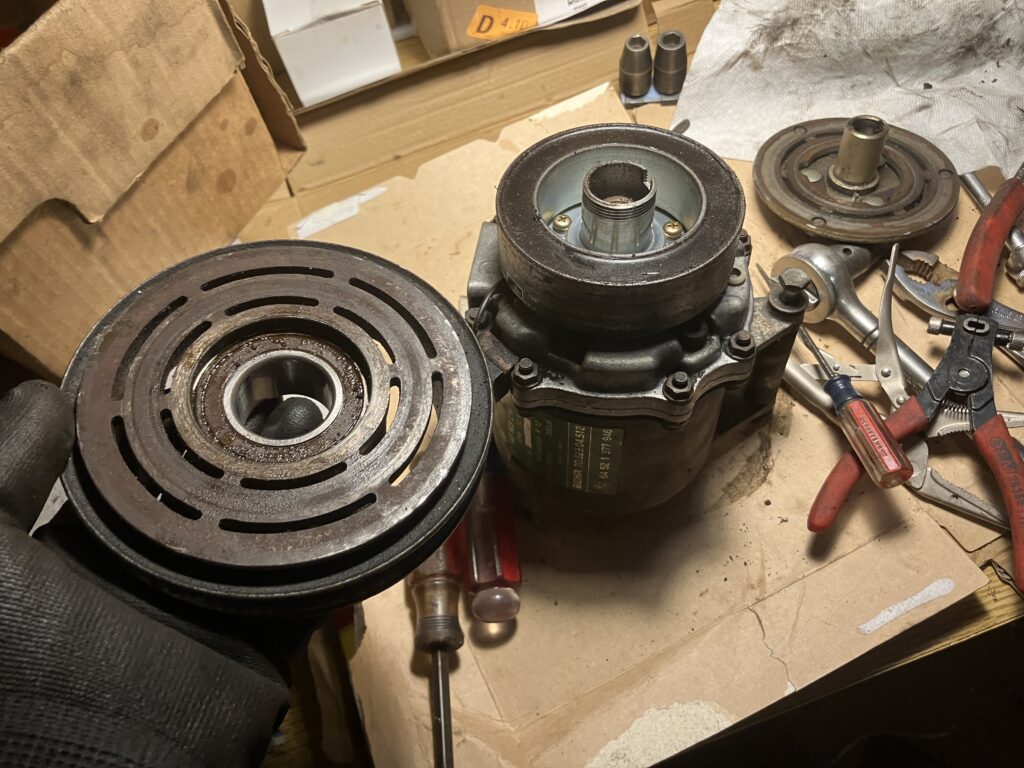
Left to right: Lower plate, pulley, coil, and upper plate connected to the compressor shaft. The coil, when energized, pulls the plates together, thus connecting the pulley to the compressor shaft and engaging the compressor.
Undo the Phillips screws holding the coil, and it exposes the top cover of the compressor housing.
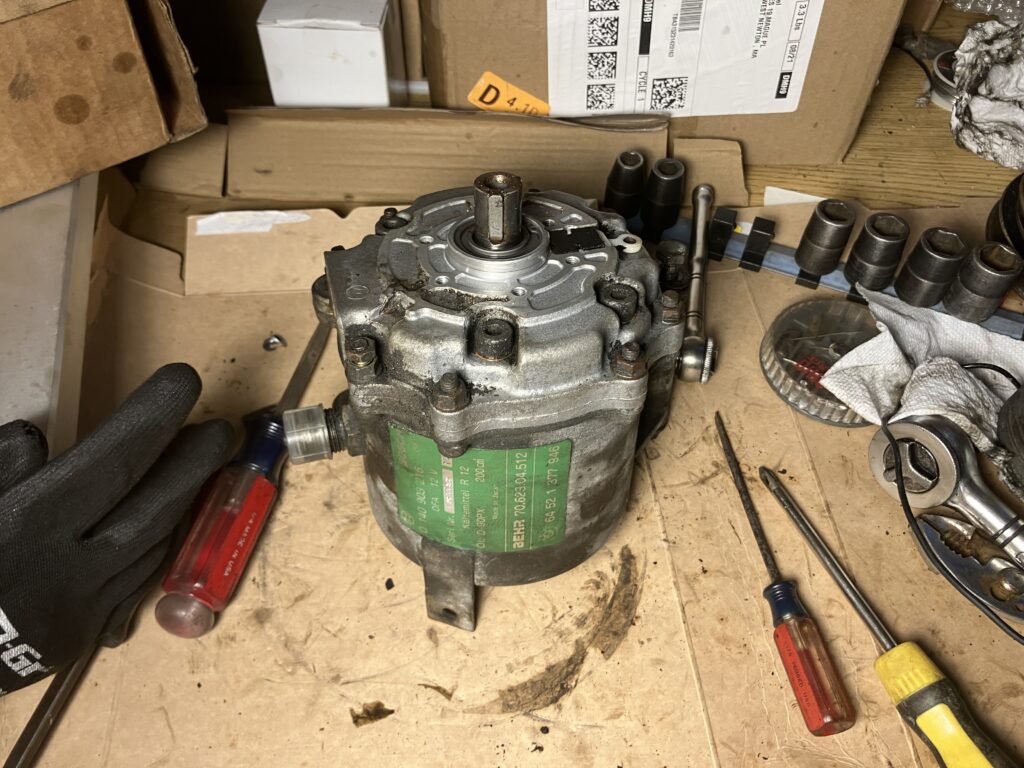
The real work begins.
The ring of 10mm nuts on the outside and 6mm Allen head bolts on the inside both need to come off. The latter were on so tight that I had to fire up the impact wrench to get them off (I hate having to fire up my 40-year-old Sears 20-gallon 2 1/2-hp compressor that lives in the unheated sheltered under-porch storage area when it is 14 degrees out). Neither the circlip nor the half-moon key in the shaft slot need to come out, at least not right now. You can see the three main compressor case seals when the cover is off.
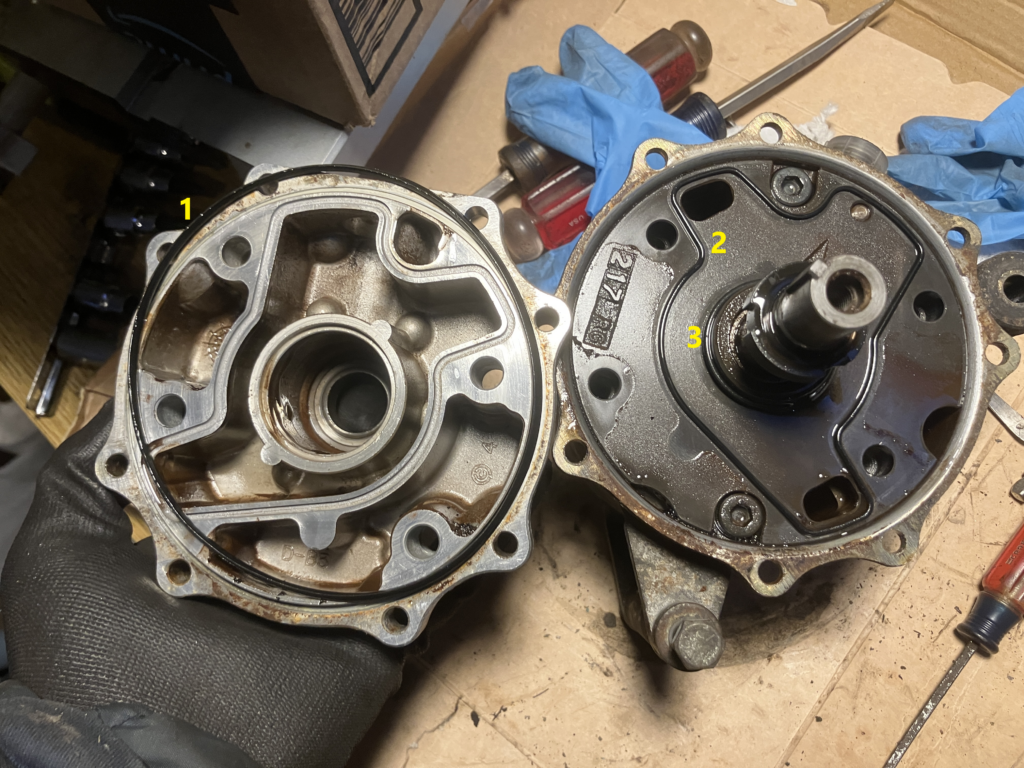
The big round seal and the irregular seal are very visible. The small round one around the base of where the shaft goes through the compressor’s body is less obvious.
Looking carefully at the photo above, you can see small bits of black particulate matter, but nothing approaching the density of what I saw in the oil. I wondered if maybe I should just rinse the partially disassembled compressor, reassemble it, and reseal it. But curiosity got the better of me, so I kept going. That meant carefully knocking the key out of the keyway on the shaft and withdrawing the odd sealing ring around it.
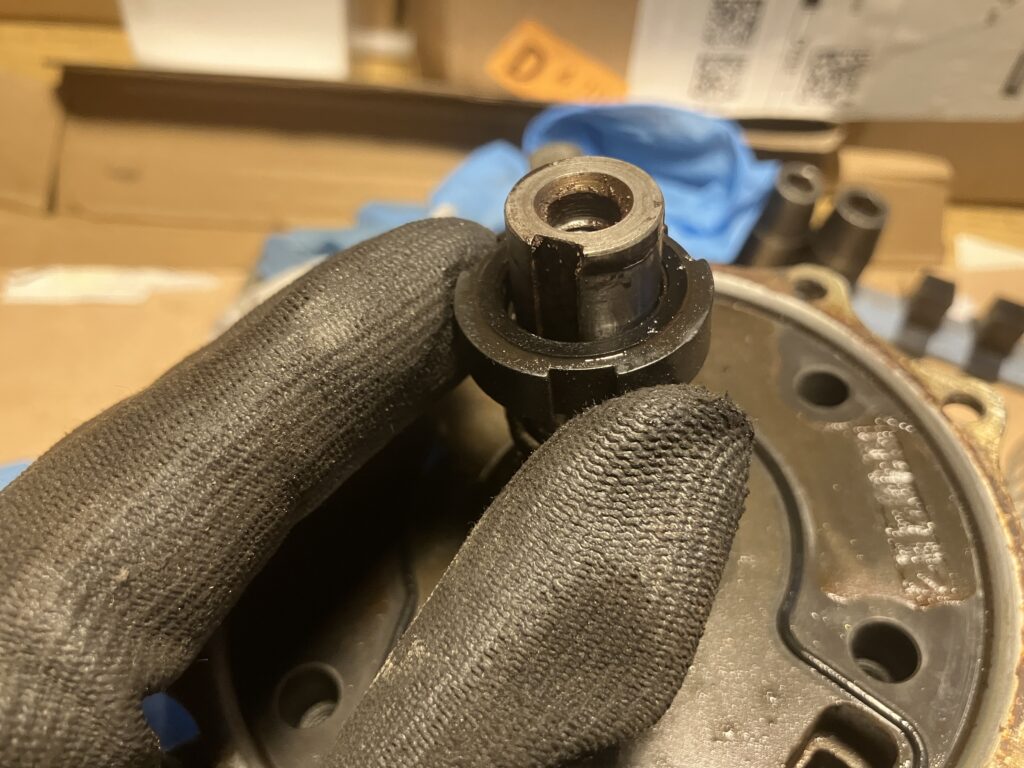
Off you go.
Remove two more 6mm bolts, and you’re at the point where you can withdraw the compressor core from its housing. The problem was that it wouldn’t budge, and I could find no documentation on how to get it to do so. I sprayed SiliKroil around the outer edge, tapped it lightly with a plastic hammer, suspended it upside down on two 2×4 sections, and repeatedly slammed it down, with the ears on the edge of the case catching the wood. It slowly gave way.
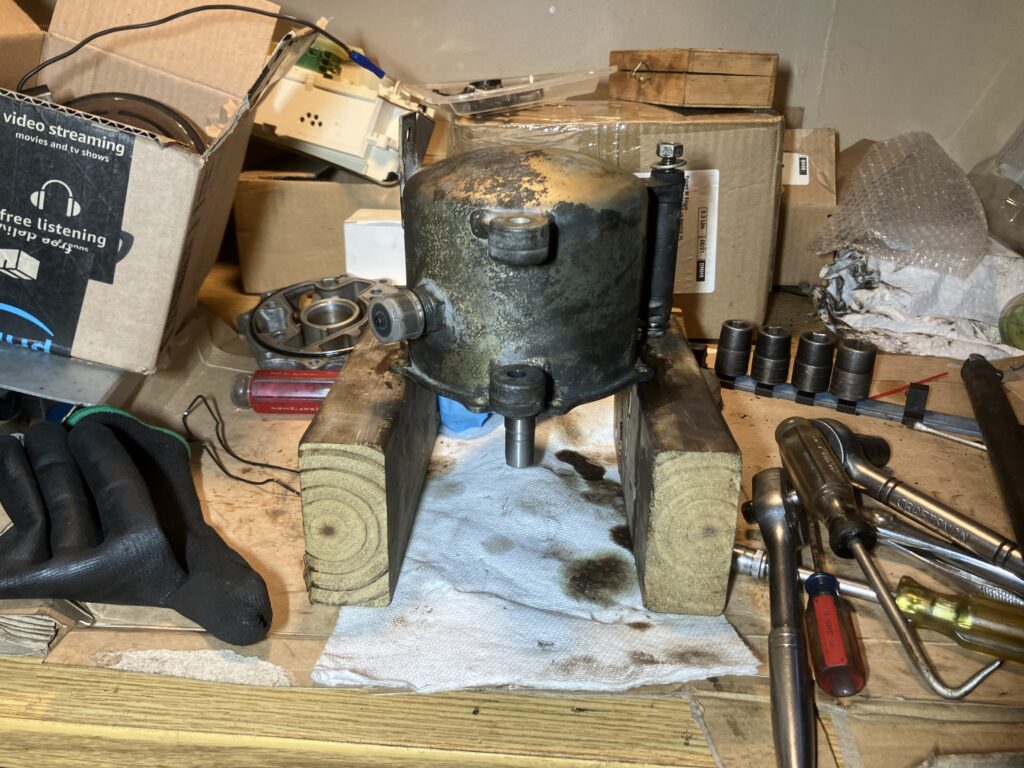
You know what they say about necessity being a mother.
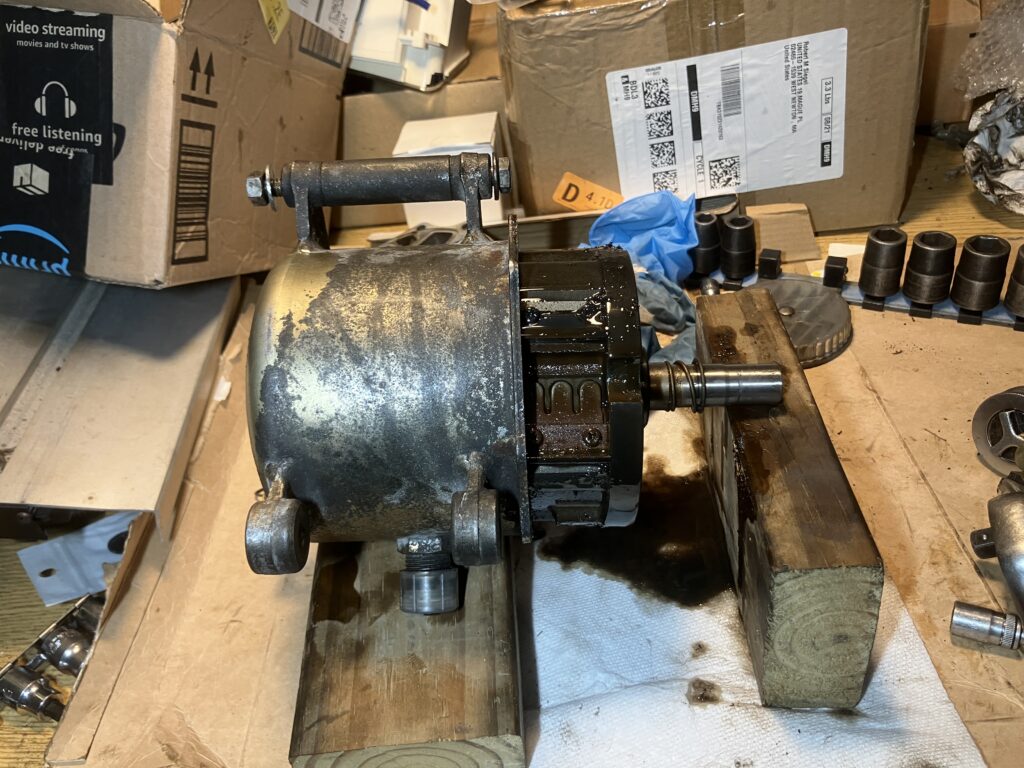
Success.
When I pulled the compressor core out of the housing, I found the motherlode of the black matter. Its former shape was unidentifiable if this was what was left of a sponge or gauze pad.
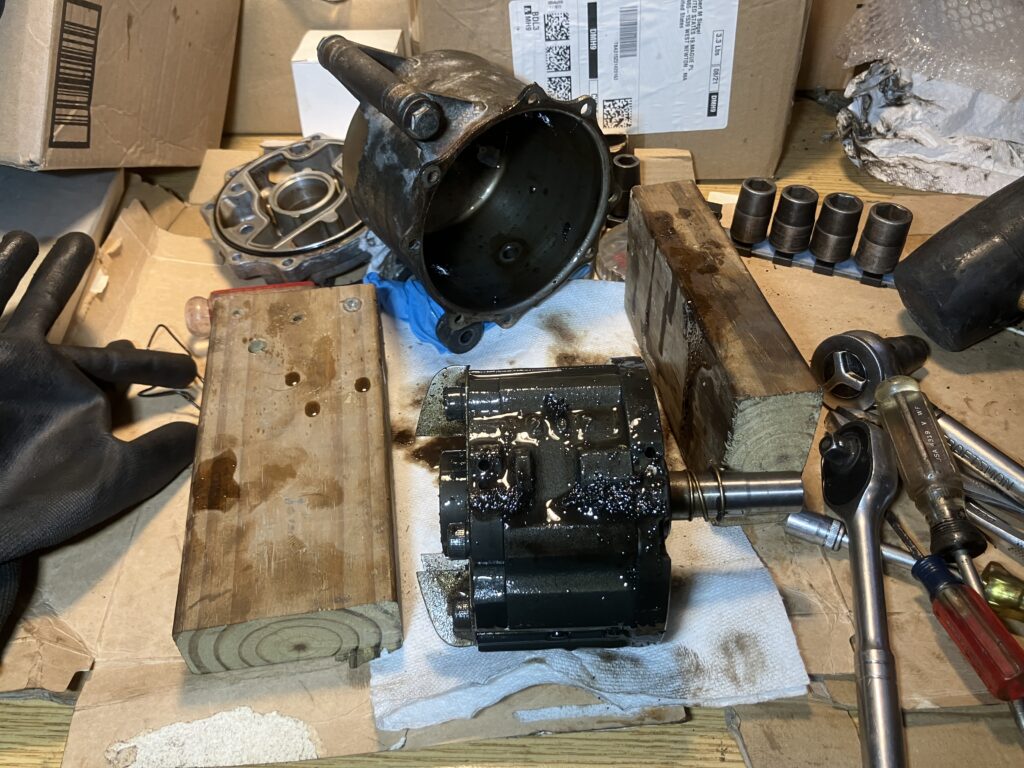
Yucccchhhh.
I took the compressor core to the parts washer, hosed it off, and then faced the same choice: Should I stop here? This was clearly the motherlode, but should I go inside the compressor core? Having the DIY post on BimmerForums was a huge advantage in that it showed me that the next steps weren’t anything to be afraid of, so… level three of Compressor Inception, right?
Six more 6mm Allen-head bolts need to come off the top.
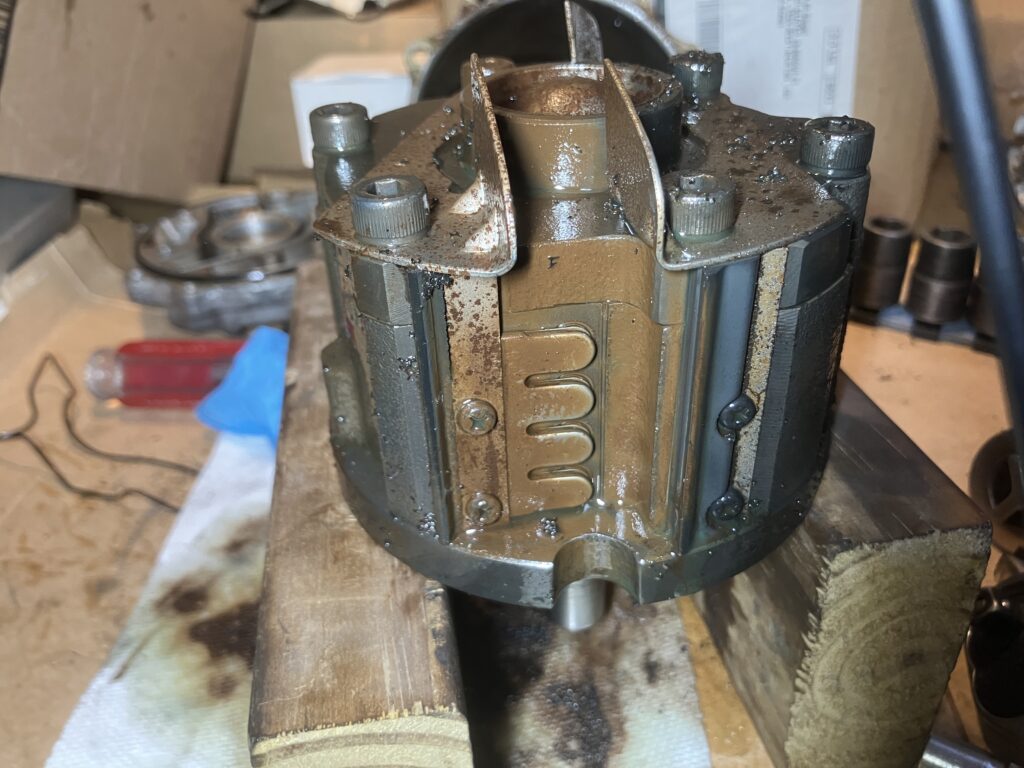
The little four-fingered thing is actually a reed valve plate. There’s one on both the inlet and outlet side. Very simple.
With the core cover off, you can see something very cool. The old upright York compressors, which looked like lawnmower engines, were old-school piston compressors. Many refer to cylindrical compressors, like a Sanden, as rotary compressors. I’m usually careful to call them “rotary-style compressors” because most have pistons inside. This one, however, is different. It’s a rotary vane compressor (I believe the term “wing cell” derives from the rotary vane design). It’s not a Wankel engine—it doesn’t have that magic triangular rotor—but you can see how it has an elongated rotary-style chamber not unlike a Wankel. As the compressor spins, the centrifugal force flung the five rotary vanes outward. It’s a metal-to-metal seal against the inner surface of the chamber, I suppose not unlike a piston ring. Rubber o-rings in the middle, both on top and underneath, appear to be there not to seal but to provide push-back to the vanes as they make their closest approach to the sides of the chamber to perform the suction, compression and discharge of the gaseous refrigerant.
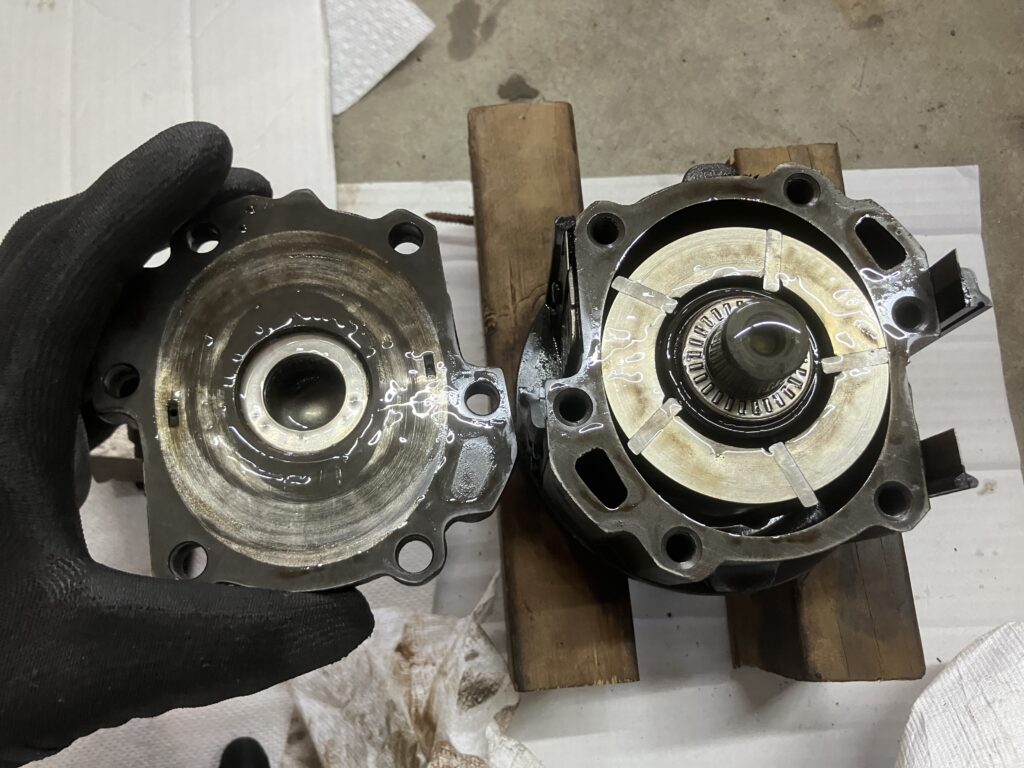
Pretty cool, right?
Although I found virtually no sponge material inside the compressor core, I carefully pulled it all apart.
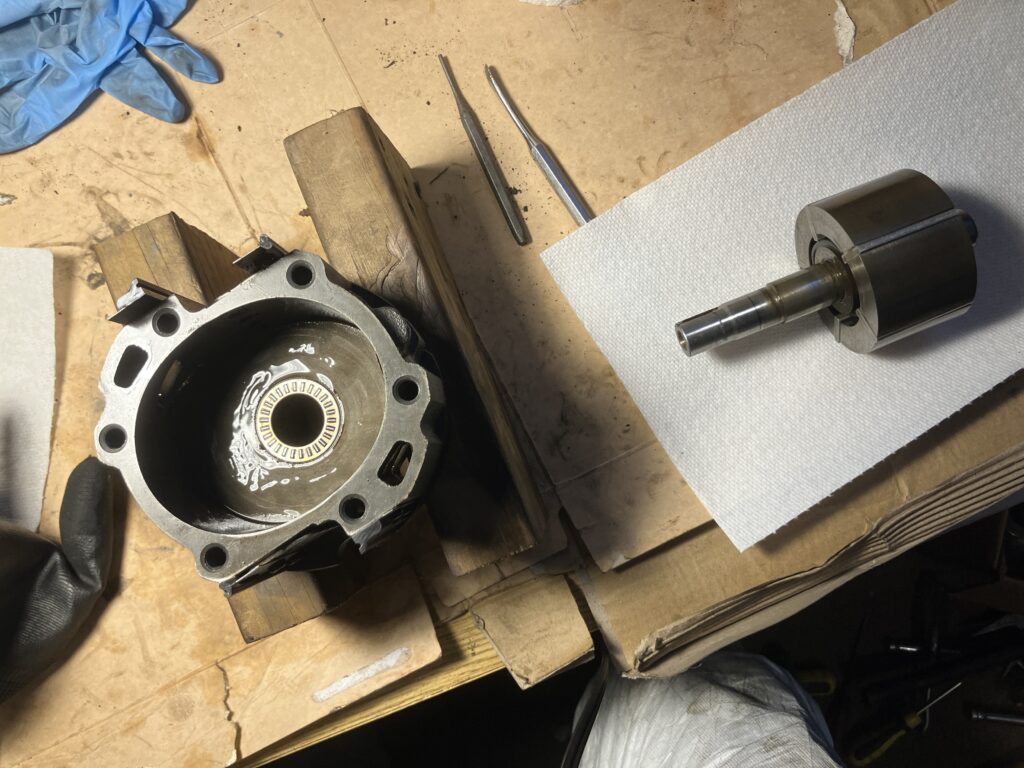
As Dire Straits said, let’s go down to the waterline.
I did find some light scoring on the face of the chamber, and am deciding whether to leave it alone or use some emery cloth to smooth it out.
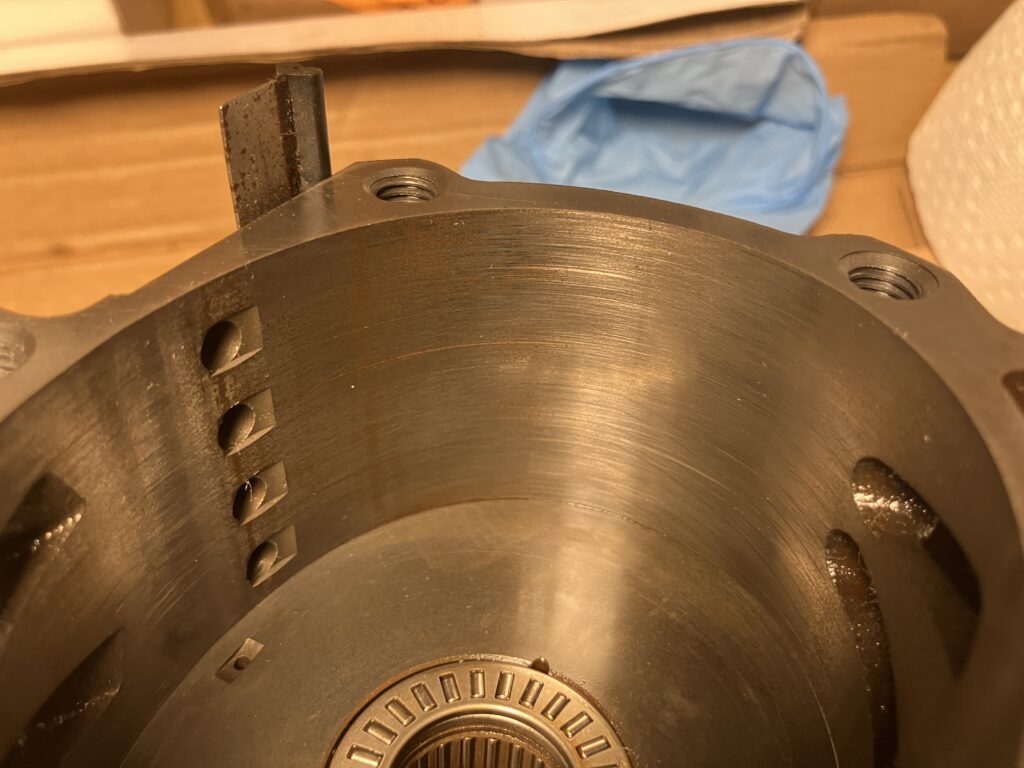
Hmm.
I decided to leave all the bearings alone, as I didn’t feel any roughness in the rotation before I disassembled the compressor. Rather than wash the entire chamber in the parts washer and risk getting crud in the bearings, I carefully wiped it out, turned it upside down, and blew the passages out with brake cleaner. Disassembly was complete.
Then, I needed to source the seals. The articles referenced above revealed that the gasket kit for the compressor cover is Sandtech MT2107, which I found on eBay for about $17 shipped.
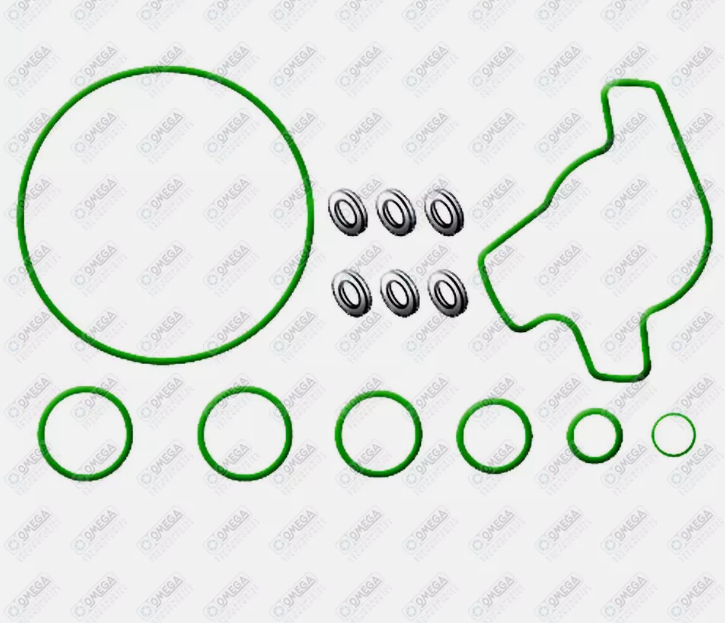
Seventeen bucks. Ya gotta love it.
However, the replacement for that odd shaft seal I mentioned above is problematic. It’s a carbon seal, and the Sandtech MT2052 replacement kit does not appear to be available anywhere. However, on close reading of the Sandtech catalog I linked to above, the kit I ordered should have in it the two o-rings that fit inside the carbon housing. As long as my carbon seal housing isn’t cracked, I should be fine.
I’d hoped that the seal kit would’ve already been here, but it’s running late. So that’s where I’ll leave things this week.
—Rob Siegel
____________________________________
All eight of Rob’s books are available on Amazon. Signed, personally inscribed copies can be ordered directly from Rob here.