On an annual basis, BMW sources about 10,000,000 light-alloy wheels for use on production vehicles. Approximately 95% of these wheels are constructed from cast aluminum, and BMW says wheels in total account for roughly 5% of supply-chain carbon dioxide emissions. Starting in 2024, however, the wheels BMW needs to build cars will be produced using sustainable practices, with renewable energy used to power operations, and the use of secondary (recycled) material in composition.
The BMW Group has signed contracts with its various wheel suppliers to ensure that they exclusively rely on renewable energy for the production of wheels starting in 2024. The Mini brand will actually be the first to offer a vehicle with sustainably-produced aluminum wheels. The second-generation Mini Countryman is set to be offered with light-alloy cast aluminum wheels made from 70% secondary aluminum (recycled material) that are produced using renewable energy. According to BMW, this combination can result in carbon emissions being reduced by up to 80% in comparison with conventional manufacturing processes.
“Green power is one of the biggest levers for reducing CO2 emissions in our supply chain. We have already signed more than 400 contracts with our suppliers, including suppliers of wheels and aluminium, requiring them to use green power,” said Joachim Post, member of the Board of Management of BMW AG responsible for procurement and the supplier network.
Aluminum is described as having good recycling properties, which means it’s easy to melt down old aluminum wheels so their material can be used in the manufacturing of new wheels. The use of recycled material alone mitigates the necessity for energy-intensive electrolysis to produce the primary raw material. However, the secondary aluminum must stand up to BMW’s standards in the areas of quality, safety, design, and mechanical properties.
Last year, BMW announced that it would begin sourcing aluminum produced using solar power from Emirates Global Aluminum (EGA), a supplier based in Dubai, United Arab Emirates. The aluminum sourced from EGA is branded CelestiAL, and is made using solar power from the Mohammed Bin Rashid Al Maktoum Solar Park near Dubai. The foundry at BMW Group Plant Landshut uses about 47,400 tons (approximately half of its annual input requirement) of CelestiAL aluminum each year.
Both BMW’s light metal foundry in Landshut and EGA are certified by the Aluminum Stewardship Initiative (ASI), which has also certified some of the production practices and suppliers related to the sustainable production of cast aluminum wheels.
Relevant to this announcement is BMW’s development of FSC-certified (Forest Stewardship Council) tires in collaboration with Pirelli. The tires will be offered as equipment on the X5 xDrive45e plug-in hybrid, and are made from natural rubber and rayon. The BMW i3 came with FSC-certified natural interior wood trim starting in 2013, and the iX is offered with it now in addition to natural leather. BMW was a partner in launching the Global Platform for Sustainable Natural Rubber (GPSNR) in 2019.—Alex Tock
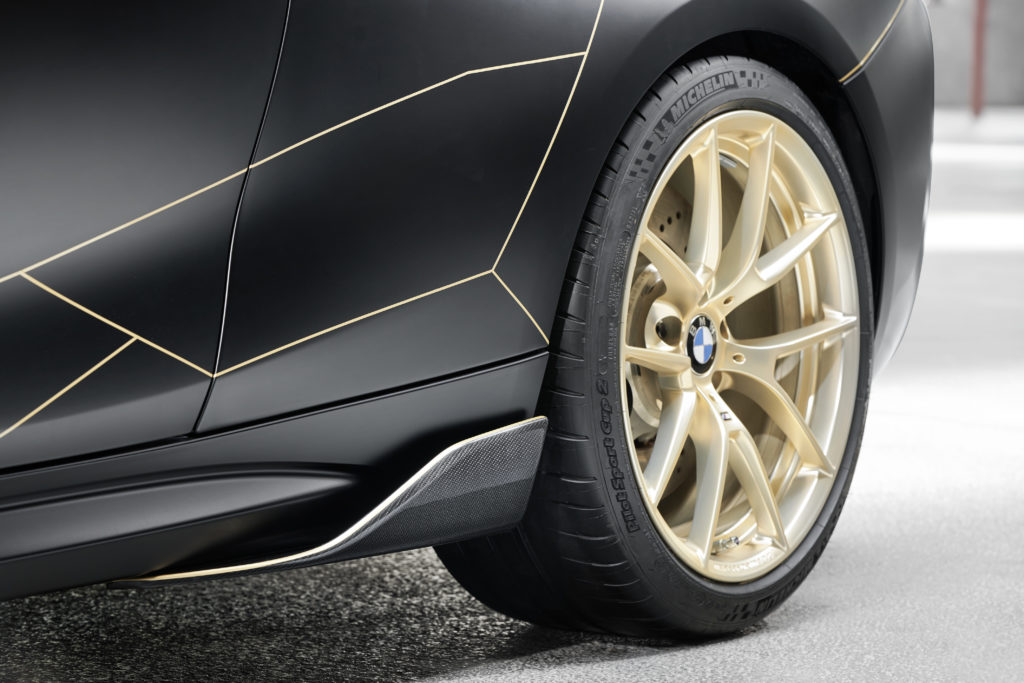
Whether or not we’ll see BMW use sustainable production practices for the manufacturing of forged wheels in addition cast aluminum designs remains to be seen.
[Photos courtesy BMW AG.]